Volkswagen Autoeuropa tenía una problemática. El tiempo y costo de las herramientas que utilizan para el ensamblado de sus partes dentro de la industria automovilística.
Para esto, siempre utilizó terceros proveedores que fabricaban sus herramientas. Este procesos de fabricación les tomaba varias semanas, especialmente cuando varios diseños y ensambles eran necesario para construir la herramienta necesaria.
Adicionalmente a esos tiempos estaban la parte burocrática, las reuniones, y las pruebas y errores hasta lograr el equipo necesario. Esto por lo general supone una detención del proceso de fabricación.
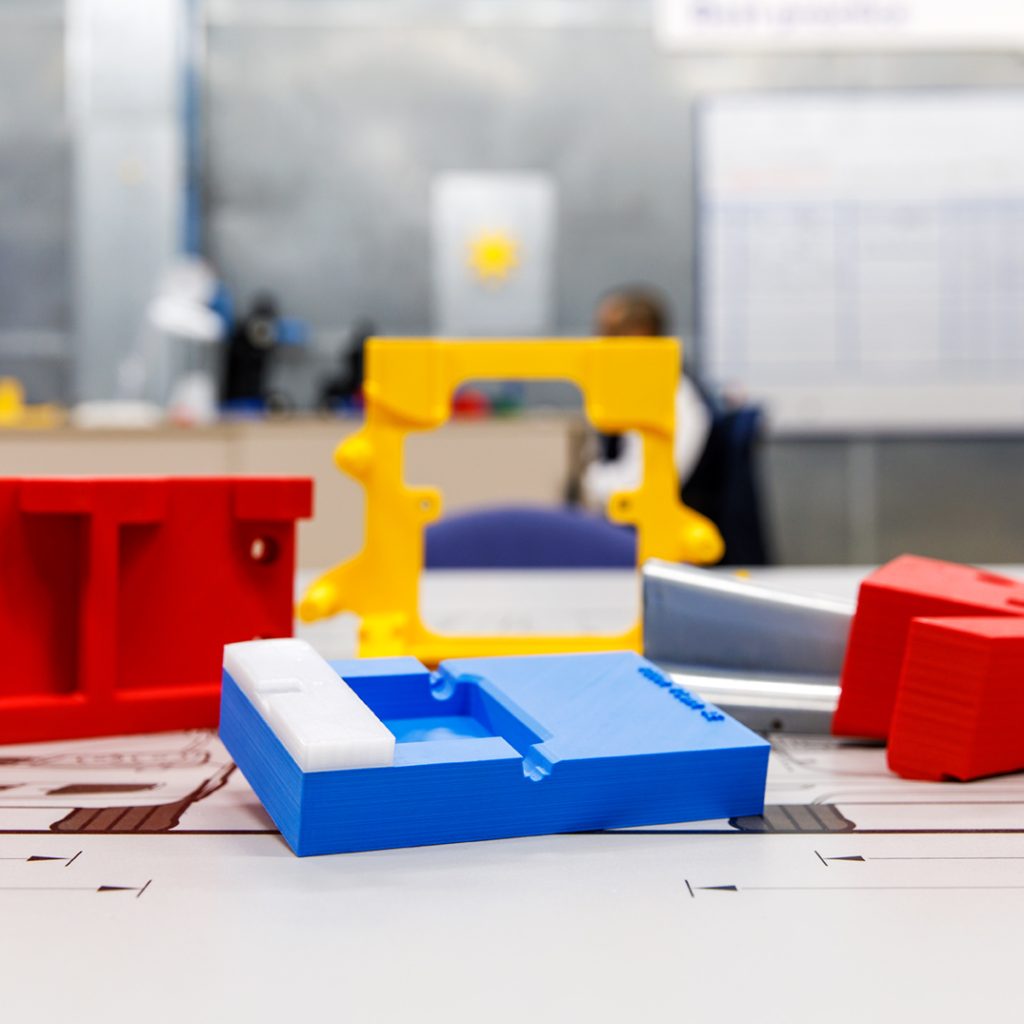
Atentos a esta problemática, allá por 2014 comenzaron con el uso de impresoras 3D de Ultimaker. El objetivo a corto plazo de la compañía era crear más prototipos, calibradores, herramientas y repuestos en la empresa, reduciendo aún más el tiempo de desarrollo y las pruebas de aceptación.
Para esto, las impresoras 3D de Ultimaker brinda esa flexibilidad y autonomía, en los procesos de mejora continua. Con esto, lograron un impacto directo en ergonomía y calidad.
Mediante el uso de impresoras 3D, construyeron herramientas, plantillas y accesorios. Con esto, Volkswagen Autoeuropa redujo la duración del ciclo de trabajo, la mano de obra y la necesidad de re trabajo sobre estos productos, al tiempo que mejoraba la ergonomía de las herramientas, su principal foco.
Actualmente el 93% de las herramientas se producen internamente. En el plazo de esos dos primeros años, el ahorro de los costes de ensamblado de herramientas subió – de 70% a 95% de ahorro. En esto, Ultimaker posibilitó a Volkswagen Autoeuropa a probar soluciones sin tener que ponerse en contacto con los proveedores, reduciendo el tiempo que les tomaba este ida y vuelta, en un promedio de ocho semanas.
La gente Volkswagen dicen acerca de esto:
“Es un proceso sencillo: simplemente convertimos nuestra idea en un archivo 3D, enviamos a la impresora 3D, procesamos la pieza, evaluamos con pruebas funcionales y terminamos implementando la idea”.
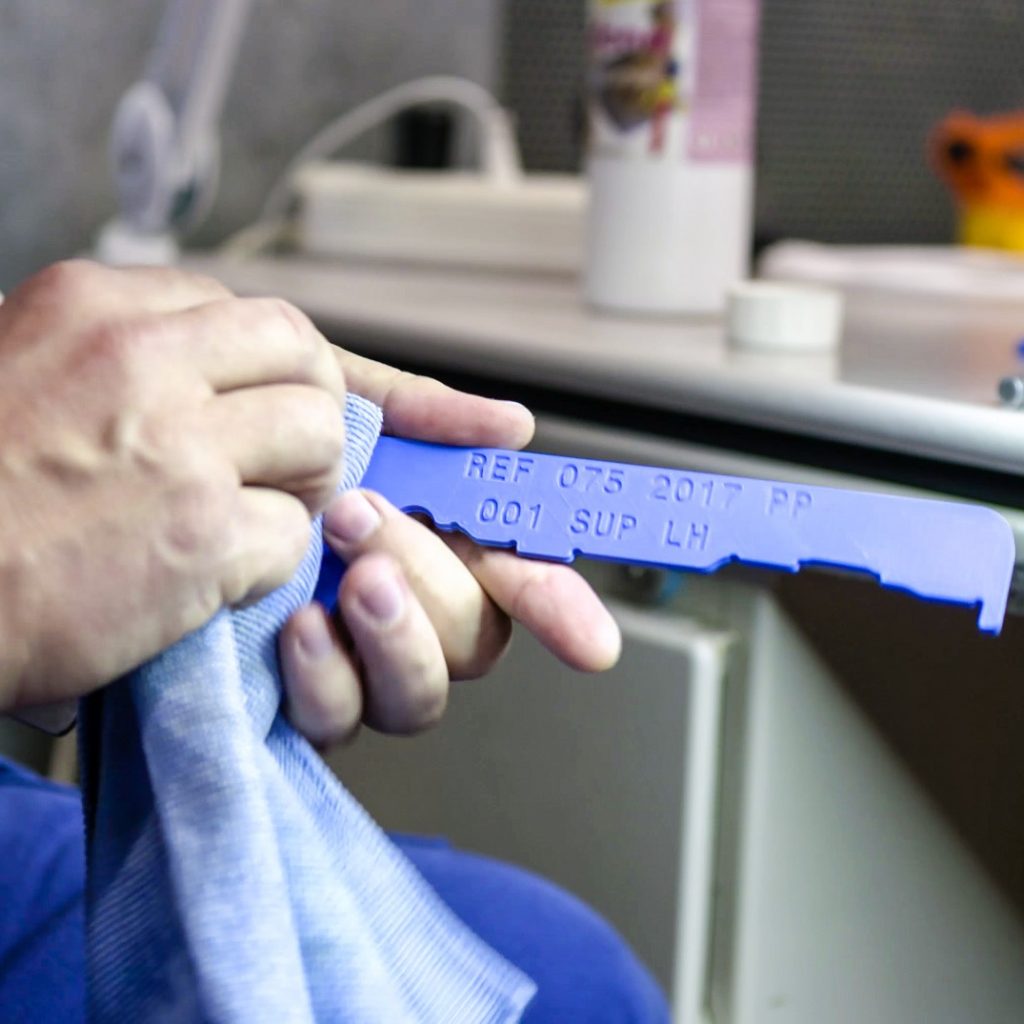
Cuando se evaluaron los costos, se detectó que esto se lograba en una décima parte del costo habitual. La compañía estima que están en camino de ahorrar 250.000 euros para finales de 2017.
A medida que fueron avanzando fueron adquiriendo una mayor cantidad de impresoras 3D, teniendo en la actualidad 7 en total. Y esperan en el futuro, buscan ampliar aún más estos beneficios – con la producción de grandes series que se aplicarán al producto final.
La reducción en el tiempo y el costo de producir prototipos llevó a un ROI más alto, a un producto de la mejor calidad, ya una mayor satisfacción del cliente. Innovando productos desde los impresos 3D, Volkswagen Autoeuropa está utilizando esto en varias aplicaciones y se consideran buenas prácticas en el grupo Volkswagen.
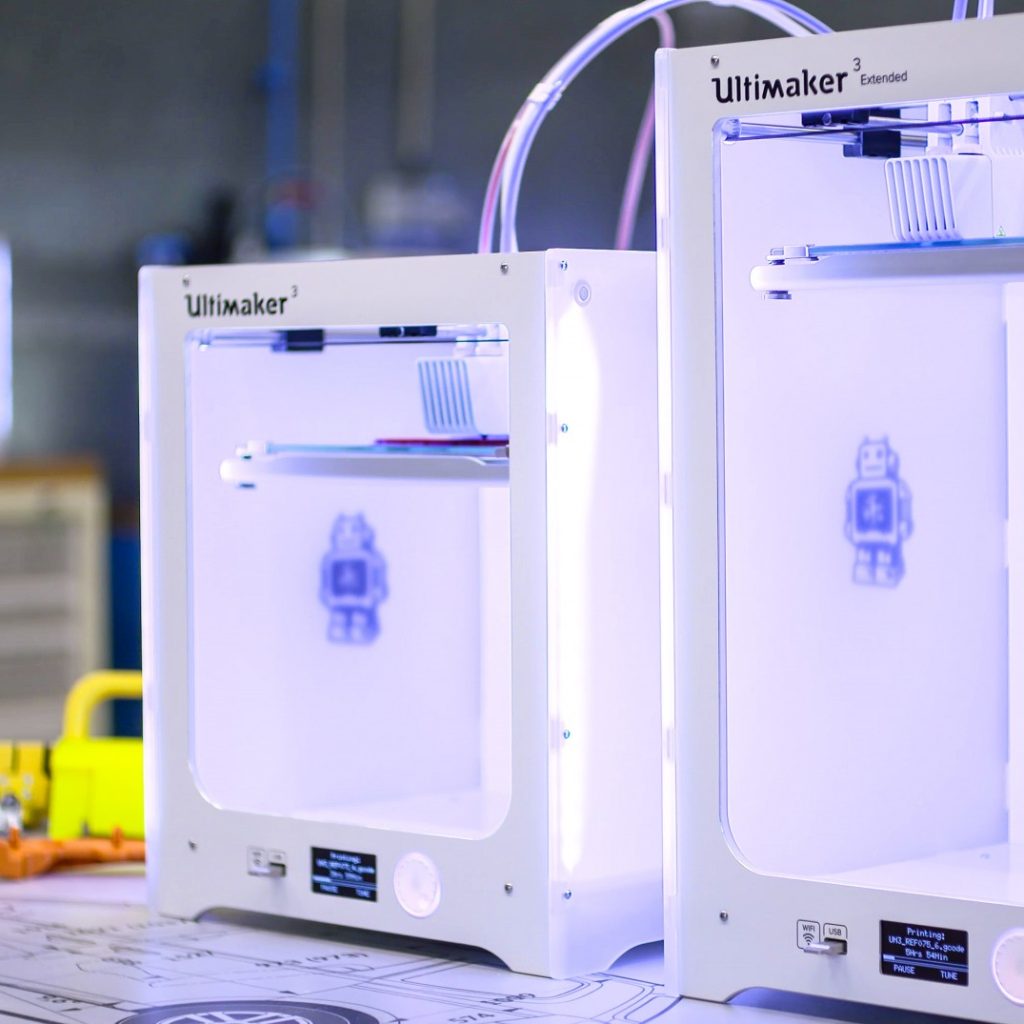
La impresión 3D les permitió probar las herramientas de construcción y montaje, reduciendo sus tiempos de desarrollo en un 95% y evitar el proceso burocrático de tratar con los proveedores. Al imprimir prototipos en casa, Volkswagen Autoeuropa logró una reducción de costes del 91% (aproximadamente 150.000 € al año en 2016). En general, con esos números, el objetivo para este 2017 es ahorrar 250.000 euros, y solamente teniendo 7 impresoras produciendo las herramientas que usan diariamente.